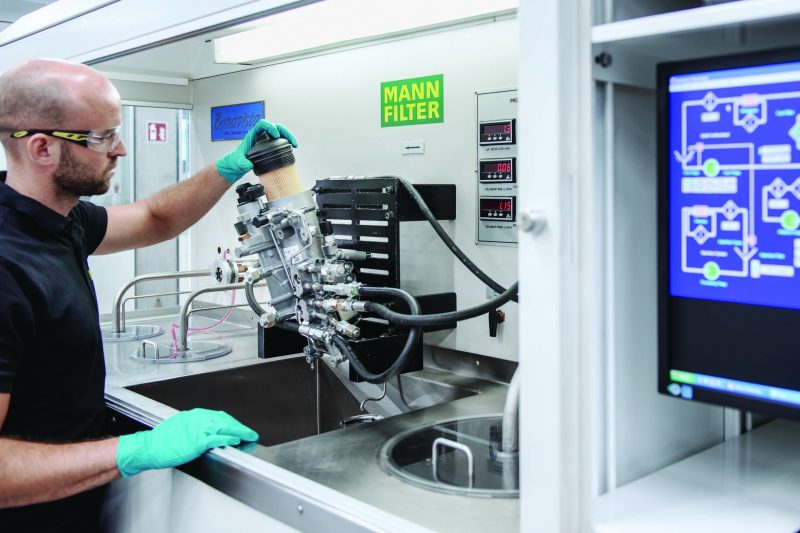
I filtri sono i silenziosi eroi dell’ingegneria automobilistica. Nascosti all’interno della vettura, non si vedono e non si sentono, e tuttavia garantiscono prestazioni costantemente elevate. MANN+HUMMEL produce 24 filtri al secondo. I prodotti sono disponibili per il mercato dell’aftermarket, con la stessa qualità di primo equipaggiamento, sotto il riconosciuto marchio MANN-FILTER. Ma da dove deriva l’elevata qualità MANN-FILTER? Dall’esterno non è sempre visibile. Solo guardando all’interno si può determinare la vera qualità di un filtro ed è per questo che MANN-FILTER esamina nel dettaglio il media filtrante del nuovo filtro carburante PU 11 001 z.
Il sottile strato del media filtrante è il cuore di ogni filtro. Svolge il lavoro principale: la pulizia del carburante. Perché se il carburante non è pulito, anche la combustione non può esserlo. MANN-FILTER fissa i propri elevati standard in termini di pulizia e prestazioni, in modo da rispettare e superare le specifiche delle case automobilistiche. Ecco perché il marchio è in grado di soddisfare le esigenze dei moderni sistemi di iniezione ad alta pressione.
Oltre 1.000 sviluppatori dalla family company lavorano costantemente a tecnologie di filtrazione ottimizzate e innovative. Per fare ciò servono conoscenze, esperienza e creatività. “I media filtranti melt-blown in cellulosa utilizzati finora non saranno più in grado di soddisfare le esigenze future dei carburanti puri. I sistemi d’iniezione moderni, caratterizzati da ugelli sottilissimi, pressioni che raggiungono i 2.500 bar e tempi di ciclo nel range dei millisecondi, sono così sensibili che anche le più piccole particelle di sporco nel carburante agiscono come proiettili e possono causare danni ingenti. Ecco perché è necessario lo sviluppo di nuovi media filtranti”, spiega il Dr. Lars Spelter, responsabile per lo sviluppo dei filtri carburante presso MANN+HUMMEL. Una di queste innovazioni è costituita dal media filtrante MULTIGRADE FMB 333, contenuto nel filtro carburante PU 11 001 z MANN-FILTER. L’obiettivo del prodotto è chiaro: aumentare il grado di separazione e la capacità di assorbimento della sporcizia, ridurre la perdita di pressione e le dimensioni.
Per ottenere ciò, gli sviluppatori hanno ideato un media filtrante composto da tre strati: uno strato in fibra completamente sintetica, che ha il compito di migliorare l’assorbimento della sporcizia. Uno strato misto in cellulosa e finissime fibre di vetro che garantisce un grado di separazione particolarmente elevato. E uno strato finale in cellulosa che funge da supporto e impedisce la fuoriuscita delle fibre di vetro.
Una volta definiti tutti i parametri, ogni nuovo prodotto deve passare al banco di prova. I test iniziano con un primo campione del media filtrante con dimensioni A4. Nel nuovo centro tecnologico ultramoderno di Ludwigsburg, un contatore del numero di particelle computerizzato misura in primo luogo il grado di separazione. Come tutti i test, anche questo è conforme alle normative ISO. Quante particelle e di quale misura passano attraverso il campione? “MULTIGRADE F-MB 333 è stato ottimizzato fino al punto in cui ha consentito il passaggio di sole 3 particelle su 1.000 da 4 micrometri. Tali particelle sono fino a 18 volte più sottili di un capello umano”, spiega Spelter. Le sottilissime fibre di vetro nonché la combinazione di materiali dei tre strati consentono un grado di separazione eccezionale di oltre il 99,7 percento per particelle fino a 4 micrometri. Nella fase successiva gli sviluppatori testano la capacità di assorbimento della sporcizia. A tal fine aggiungono fuliggine alla sostanza di prova. In questo caso ogni nuovo media filtrante deve dimostrare di non bloccarsi prematuramente nonostante le numerose particelle di sporcizia separate. Questo metodo di prova riflette il funzionamento sul campo in modo più realistico rispetto ad altri test conformi a ISO.
Se tutti i requisiti sono soddisfatti, si passa a definire lo stabilimento produttivo adatto fra quelli presenti nella propria rete mondiale. Si avvia un test su scala ridotta. Gli specialisti della lavorazione e i tecnici si occupano della disposizione delle pieghe, del taglio del soffietto, dell’indurimento, dell’incollaggio e del collegamento del media filtrante con la piastra terminale. Vengono così realizzati manualmente da 20 a 30 filtri campione per superare i banchi di prova e i successivi test di Ludwigsburg, nel caso del MULTIGRADE FMB 333. Qui si controlla se le varie interfacce tra il soffietto e le piastre terminali e la saldatura del soffietto sono a tenuta e configurate in modo stabile. Se i risultati non sono ancora soddisfacenti, è necessario modificare i materiali e la lavorazione e sottoporli a ulteriori test. Già in questa fase gli esperti prendono decisioni importanti per la successiva produzione in serie. Ad esempio, come collegare il media filtrante con la piastra terminale. Da una serie di possibilità, nel caso del filtro PU 11 001 z MANN-FILTER la scelta è ricaduta infine sulla saldatura a infrarossi. Per la saldatura del soffietto di un media filtrante vi sono ancora più possibilità. In questo caso la saldatura tramite incollaggio è stata considerata la scelta migliore.
Nell’ultima fase si torna allo stabilimento di produzione, dove si avvia un tentativo di produzione in grande serie. Impianti composti da rulli giganteschi producono circa una tonnellata del nuovo media filtrante, diverse centinaia di elementi filtranti vengono realizzati alle condizioni per la produzione in serie. Tagli, pieghe, indurimento e altro ancora: ora il nuovo prodotto deve dimostrare che la lavorazione è pronta al funzionamento continuo e che i processi sono stabili. Solo quando l’applicazione raggiunge il livello adatto alla produzione in serie, lo stabilimento di produzione e il reparto di sviluppo danno il via libera. “Il lavoro di sviluppo è particolarmente impegnativo, richiede grandi conoscenze e un grande impiego di personale. Tuttavia affrontiamo volentieri questo impegno per poter offrire ai nostri clienti prodotti MANN-FILTER innovativi e di qualità elevata anche in futuro e per poter continuare a imporre nuovi standard nel settore della filtrazione”, afferma Spelter.
Condividi l'articolo
Scegli su quale Social Network vuoi condividere